top of page
Automatic SandBlasting Systems & Spare Parts

Barrel SandBlasting Machine
Pangborn Barrel Blast Machine’s tumbling action, provided by the endless rubber or metal internal conveyor, ensures all surfaces of the work piece are cleaned in one loading. The heavy-duty Pangborn Barrel Blast Machine is exclusively designed to thoroughly clean all types of castings, forgings, weldments, heat-treated work, and stampings. Our barrel blast machines are designed to process a variety of work pieces that can be tumbled, and the endless conveyor belt and lateral round place creates a trough in which work pieces are treated. The loading and unloading process is specifically geared to the work piece and workspace requirements. The optimum adjustment of the blast capacity is specified to the required blasting result. The tumbling action provided by the rubber or metal conveyor ensures that all surfaces of the work piece are cleaned in a single batch. Pangborn offers a variety of barrel sizes depending on the size of the work pieces being blasted. Most often, larger machines are used for high output cleaning on medium sized castings, forgings, or fabricated work pieces. Barrel Blast Machines allow for a high volume of work pieces to be processed in a small working area. Highly configurable, these machines can be delivered with a rubber or metal conveyor, vibratory conveyor, magnetic separator, hydraulic loader, unloading conveyor, and dust collector.
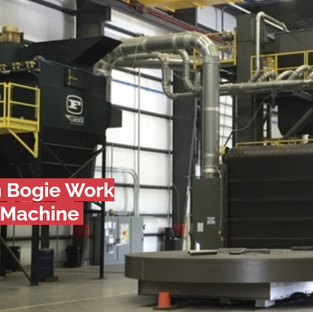
Bogie Work Car Blast Machines
Pangborn Bogie Work Car Blast Machines are ideal for the treatment of large and heavy castings and forgings. Pangborn Bogie Work Car Blast Machine is ideal for large and heavy castings and forgings ranging from 5 to 200 tons, such as marine engines, energy and power generation components, and wind towers. Blast wheels are installed on oscillating panels to optimize abrasive streams. The use of the transport bogie with a rotary table allows work pieces to be loaded and unloaded outside the blast chamber by cranes and moved safely into and out of the machine. The moving portal for blast wheel arrangements allows for reduced installation space when blasting very large work pieces. Once loaded, the work is first shot blasted by blast wheels, and if necessary, additional air blasting is performed manually by an operator within the blast chamber. This enables areas of the work piece to be cleaned that otherwise would not be cleaned by the blast wheel and shot blasting process.

Continuous Barrel Machine
The Pangborn Continuous Barrel Machine line is a reliable and cost-effective solution for automatic handling of heavy duty mixed work piece loads or when customers have a large and continuous flow of work to be cleaned. Blast cleaning cycles are fully adjustable with programs to modify process parameters (including abrasive flow and passage speed) depending on the needs of the line or the work pieces. Pangborn offers a variety of barrel sizes to accommodate a wide range of work piece sizes being blasted. The Continuous Barrel Machine can blast up to 37 tons of per hour. Several loading and unloading solutions are available.
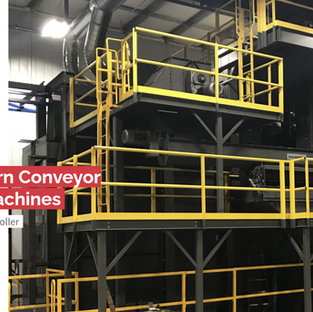
Conveyor Blast Machines
Pangborn Conveyor Blast Machines are a diverse line of machines designed to provide faster throughput and maximum blast coverage for a continuous flow of work pieces. The Pangborn Conveyor Blast Machines are offered in a wide range of machine types for different production rates, work pieces of different sizes, and is easily integrated into existing production lines. The Continuous Belt Conveyor Blast Machine is ideal for symmetric, sensitive work pieces. Our Roller Conveyor Blast Machines are the right solution for heavy plates and structural shapes. Lastly, our Monorail Conveyor Blast Machines are preferred by customers who are blasting heavy work pieces at a high pass through rate. The Pangborn Vertical Descaling Systems provide high volume production and cost effective performance for deburring, cleaning, descaling, or etching of plate, structurals and fabrications. Customized work handling solutions (monorail, crane, and roll conveyors) allow for maximum flexibility. Pangborn Combination Descaling Systems maximize the cleaning of smaller products by providing high volume production and cost effective performance for deburring, cleaning, descaling, deflashing or etching. It is extremely versatile for efficient blast coverage.

RotoDrum Blast Machines
Pangborn’s RotoDrum Blast Machines are durable rotating drum machines with versatile drum design to allow efficient tumbling of work pieces with no pinch points, catch points, or sharp edges.
Pangborn’s RotoDrum Blasting Machines are the heaviest and most durable rotating drum machines available. Versatile, solid manganese drums allow efficient tumbling of work pieces with no pinch points. The solid welded drum is manufactured with up to ¾” (19 mm) thick manganese steel (zero catch points, no sharp edges to nick or damage work pieces). The loading is carried out via the loading bucket feeder. The capacity of the feeder corresponds to that of the blasting machine. To prevent the discharge or loss of blasting abrasives, the loading duct is equipped with a rubber pendulum seal. The machine blasts the work pieces in the drum with a single blast wheel positioned on the loading door. The bottom of the drum is designed to ensure that rotation of the batch is in both longitudinal and radial directions. When loading the work pieces into the drum, the loading door is opened upwards. When unloading the work pieces, the drum is opened downwards so parts empty onto a vibration conveyor chute. Superior design, quality, and rugged construction make the Pangborn RotoDrum Blast Machines extremely reliable and easy to maintain. Pangborn’s RotoDrum Blast Machines are cost-effective and space-saving rotating drum systems. Versatile, solid manganese drums allow efficient tumbling of work pieces with no pinch points.
Pangborn’s RotoDrum Blasting Machines are the heaviest and most durable rotating drum machines available. Versatile, solid manganese drums allow efficient tumbling of work pieces with no pinch points. The solid welded drum is manufactured with up to ¾” (19 mm) thick manganese steel (zero catch points, no sharp edges to nick or damage work pieces). The loading is carried out via the loading bucket feeder. The capacity of the feeder corresponds to that of the blasting machine. To prevent the discharge or loss of blasting abrasives, the loading duct is equipped with a rubber pendulum seal. The machine blasts the work pieces in the drum with a single blast wheel positioned on the loading door. The bottom of the drum is designed to ensure that rotation of the batch is in both longitudinal and radial directions. When loading the work pieces into the drum, the loading door is opened upwards. When unloading the work pieces, the drum is opened downwards so parts empty onto a vibration conveyor chute. Superior design, quality, and rugged construction make the Pangborn RotoDrum Blast Machines extremely reliable and easy to maintain. Pangborn’s RotoDrum Blast Machines are cost-effective and space-saving rotating drum systems. Versatile, solid manganese drums allow efficient tumbling of work pieces with no pinch points.
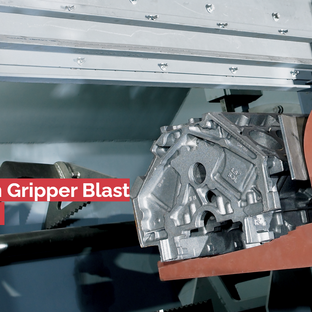
Gripper Blast Machines
Pangborn Gripper Blast Machines are the perfect surface cleaning machines for engine blocks and heads, grey iron, and aluminum.
Pangborn Gripper Blast Machines offer high volume production and minimal or no-tooling changes while processing a large volume of different size and configuration engine blocks, crank cases, gear housings, manifolds, heads, transmission cases, and other vehicle parts. Cleaning deep cavities in a cast iron or light metal casting quickly and cost effectively has always presented a challenge to companies in the automotive and off-highway vehicle industries. The size and weight of engine block and head components, as well as the presence of blind passages and internal cavities, make cleaning much more complicated.
When high volume production, flexibility, efficiency, minimal down-time, and cost-effective technical solutions are required, the fully automatic Pangborn Gripper Blast Machines are the preferred choice. The Gripper Blast Machines clean engine blocks in varying sizes – from 4 cylinders to V10 diesels. The hydraulic load/unload mechanism is equipped with positive stop location to accurately position parts in the gripper. Depending on work piece configuration, the gripper rotation can be programmed to achieve the desired coverage and an improved cleaning efficiency on specific areas. The machine is equipped with a special system designed to rotate work pieces on one or two axes to evacuate residual abrasives after discharging. Advanced solutions for work piece handling are also available. All sides of the work piece are exposed to blasting, and the gripper jaw rotation allows for proper abrasive drainage. Gripper blast machines from Pangborn are tailored to each customer’s unique requirements and specifications.
Pangborn Gripper Blast Machines offer high volume production and minimal or no-tooling changes while processing a large volume of different size and configuration engine blocks, crank cases, gear housings, manifolds, heads, transmission cases, and other vehicle parts. Cleaning deep cavities in a cast iron or light metal casting quickly and cost effectively has always presented a challenge to companies in the automotive and off-highway vehicle industries. The size and weight of engine block and head components, as well as the presence of blind passages and internal cavities, make cleaning much more complicated.
When high volume production, flexibility, efficiency, minimal down-time, and cost-effective technical solutions are required, the fully automatic Pangborn Gripper Blast Machines are the preferred choice. The Gripper Blast Machines clean engine blocks in varying sizes – from 4 cylinders to V10 diesels. The hydraulic load/unload mechanism is equipped with positive stop location to accurately position parts in the gripper. Depending on work piece configuration, the gripper rotation can be programmed to achieve the desired coverage and an improved cleaning efficiency on specific areas. The machine is equipped with a special system designed to rotate work pieces on one or two axes to evacuate residual abrasives after discharging. Advanced solutions for work piece handling are also available. All sides of the work piece are exposed to blasting, and the gripper jaw rotation allows for proper abrasive drainage. Gripper blast machines from Pangborn are tailored to each customer’s unique requirements and specifications.

Hanger Hook Blast Machines
Pangborn Hanger Hook Blast Machines are versatile blast cleaning machines for mixed loads of medium and large work pieces that frequently include fragile or irregularly shaped work pieces.
Pangborn’s Hanger Hook Blast Machines are the ideal all-purpose blasting machines. They are designed to handle mixed loads of medium and large components as well as loads with fragile or irregularly shaped work pieces. They are specifically designed to thoroughly clean work that cannot touch. There is no movement between the work and no part-on-part contact ensuring complete blast coverage without tumbling damage or tangling parts. While a variety of sizes and configurations are available, a standard hook blasting machine has a generous work cylinder. Standard models come with three blast wheels, and more can be added as necessary for even greater coverage. A Hanger Hook machine ensures better abrasive coverage by rotating or spinning the hook under the abrasive wheel streams while stopping in multiple positions. The ergonomics of work piece loading is improved with lifting hooks and optional self-powered trolleys. For automatic operation sequences or integration of the shot blast machine into a continuous production line, loading and unloading can be performed without operator assistance. In this case, an industrial robot is used which also serves to link the individual manufacturing sequences. Versatile, economical, and reliable, the Hanger Hook Blast Machine is designed as an all-purpose blast cleaning unit.
Pangborn’s Hanger Hook Blast Machines are the ideal all-purpose blasting machines. They are designed to handle mixed loads of medium and large components as well as loads with fragile or irregularly shaped work pieces. They are specifically designed to thoroughly clean work that cannot touch. There is no movement between the work and no part-on-part contact ensuring complete blast coverage without tumbling damage or tangling parts. While a variety of sizes and configurations are available, a standard hook blasting machine has a generous work cylinder. Standard models come with three blast wheels, and more can be added as necessary for even greater coverage. A Hanger Hook machine ensures better abrasive coverage by rotating or spinning the hook under the abrasive wheel streams while stopping in multiple positions. The ergonomics of work piece loading is improved with lifting hooks and optional self-powered trolleys. For automatic operation sequences or integration of the shot blast machine into a continuous production line, loading and unloading can be performed without operator assistance. In this case, an industrial robot is used which also serves to link the individual manufacturing sequences. Versatile, economical, and reliable, the Hanger Hook Blast Machine is designed as an all-purpose blast cleaning unit.
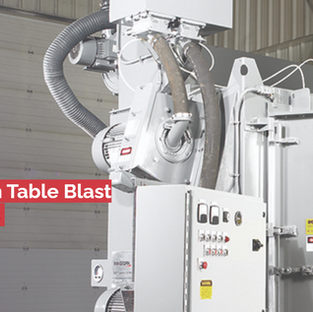
Table Blast Machines
Pangborn Table Blast Machines combine superior design with rugged construction in a fully integrated table system to handle larger and/or more fragile castings. Superior design, quality, and rugged construction make the Pangborn Table Blast Machines reliable and efficient to maintain. They are specifically designed to thoroughly clean batches with different sizes or work pieces that cannot touch. Work pieces are loaded on a table or on satellites fixed to a table prior to entering the blast chamber. There is no movement between the work and no part-on-part contact. Several work pieces can be blasted or cleaned simultaneously making Pangborn Table Blast Machines a good choice for cleaning a variety of work pieces together. Our machines come in a number of sizes and configurations depending on the customer’s needs. The configuration of options in the standard line result in several specific solutions ranging from a single table machine to a table machine with multiple satellite arrangements for applications in foundries, forges, automotive, heat treatment industries, and more.
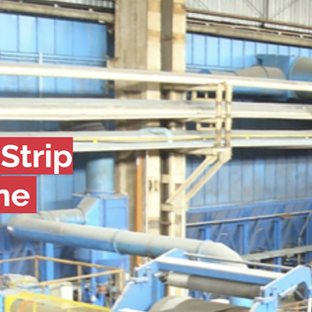
Steel Strip Descaler Machines
Pangborn Wire Descaling Blast Machines are designed for customers who want a versatile machine that can de-scale wire from 0.08 – 3.14 in (2 – 80 mm) in round, square, or hexagon shapes. Pangborn’s Wire Descaling Blast Machines are designed for customers who want a versatile machine that can process wire from 0.08 – 3.14 in (2 – 80 mm) in a continuous operation. The blast chamber is designed with blast wheels positioned around the circumference of the wire to be processed, allowing for a continuous throughput pass. The result is thorough blast coverage with a relatively quick processing time.

Anodes / Carbon Butts Cleaner Machine
The Pangborn Anodes / Carbon Butts Cleaner Machine is specifically designed for reconditioning blasting of spent anodes in the primary aluminum production process to remove cryolite, fluorite, and aluminum. The Pangborn Anodes / Carbon Butts Cleaner is manufactured in several models to accept three (3) to six (6) pins, single, or double anodes. Work pieces are conveyed under blast streams in-line or rotating and suspended on a power-free conveyor. The machine can be equipped with up to six (6) wheels – 30 HP (22 kW), arranged on one or both sides of the blasting cabinet. These options are determined based on the customer’s requirements making sure to match the heaviest finishing parameters required by this kind of process. Depending on the customer’s needs, several blasting solutions are available including treatment of baked anodes, steel stubs, cast thimbles, and cathode bars.

Crankshaft Descaler Machines
Pangborn Crankshaft Descaler Machines are ideally suited to treat cast or forged crankshafts at a high production rate. The parts are loaded on a table/carousel fitted with rotating disc supports prior to entering the blast chamber. Pangborn Crankshaft Descaler Machines can be designed to incorporate one (1) to three (3) blasting stations, a loading/unloading station, and a table diameter to meet the crankshaft length, including large size crankshafts. The machine can be equipped with up to six (6) 60HP (45kW) blast wheels arranged on the top of the cabinet. When needed, a robot for loading, unloading, and feeding step V conveyors can be included.

Coil Spring Shot Peening Machines
The Pangborn Spring Shot Peening Machines are specifically designed for peening leaf springs in non-stressed and pre-stressed conditions (stress-peening).
The stress peening process:
- Leads to significant improvement of the mechanical properties of work pieces
- Serves to extend the stress-load limit of workpieces significantly
- Permits design of light weight components
- Increases the fatigue strength of springs between 20% and 100%
- Compensates manufacturing related surface defects
The stress peening process:
- Leads to significant improvement of the mechanical properties of work pieces
- Serves to extend the stress-load limit of workpieces significantly
- Permits design of light weight components
- Increases the fatigue strength of springs between 20% and 100%
- Compensates manufacturing related surface defects
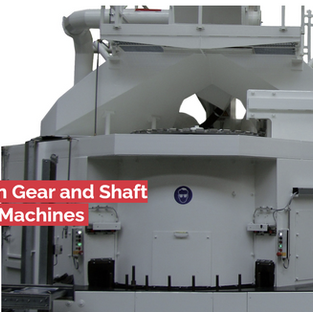
Gear and Shaft Shot Peening Blast Machines
Pangborn Gear and Shaft Shot Peening Blast Machines are the ideal solution for dynamically stressed parts of transmission components such as gears and shafts. Pangborn has served the automotive industry for decades, providing top quality blast machines and the industry’s finest gear and shaft peening machines that produce consistent, sustained results. In addition to the automotive industry, Pangborn also has a strong leadership presence in the aerospace, defense, agriculture, forge, and railway industries. Peening performance is configured to the ideal settings needed to guarantee both the blasting result as well as efficient use of energy and operating material. Abrasive discharge is concentrated for optimum shot peening performance. Customer production requirements establish the need for manual or automatic loading and unloading of work pieces. Blasting machines are equipped with two (2) to four (4) blast wheels that result in a throughput of up to 13,500 cycles per day. The variety and flexibility of Pangborn’s peening solutions ensures each customer gets exactly what is needed to address their needs.

Wire Mesh Belt Blast Machines
Pangborn Wire Mesh Belt Blast Machines can blast heavy duty small to medium sized work pieces as well as fragile castings. The blast chamber is bombarded with abrasive stemming from wheels situated above and below the work for maximum coverage.
Pangborn Wire Mesh Belt Blast Machines are a versatile option designed to blast clean work pieces on two sides in one pass through. Whether it’s for heavy duty foundry applications or thin and fragile castings, our Wire Belt Mesh Blast Machines can handle any job.
The blast chamber is bombarded with abrasive stemming from wheels situated both above and below the work as it passes through the chamber. The result is complete blast coverage with superior one pass continuous cleaning without damaging work pieces.
Pangborn Wire Mesh Belt blast machines, specifically engineered for heavy duty applications in foundry, are equipped with a lower scalping deck and designed in accordance with heavy duty usage philosophy.
Our Wire Mesh Belt blast machines can blast work pieces that require a smooth or shockless pass through, such as flat, thin-walled, and fragile iron or aluminum alloy castings. Due to the position of blast wheels, bending of thin-walled work pieces and tilting of small light parts is avoided. Our machines are also designed to handle the high temperatures of work pieces that have been heat treated.
Pangborn Wire Mesh Belt blast machines provide high-volume, cost effective performance for deburring, cleaning, descaling, deflashing, and etching.
Pangborn Wire Mesh Belt Blast Machines are a versatile option designed to blast clean work pieces on two sides in one pass through. Whether it’s for heavy duty foundry applications or thin and fragile castings, our Wire Belt Mesh Blast Machines can handle any job.
The blast chamber is bombarded with abrasive stemming from wheels situated both above and below the work as it passes through the chamber. The result is complete blast coverage with superior one pass continuous cleaning without damaging work pieces.
Pangborn Wire Mesh Belt blast machines, specifically engineered for heavy duty applications in foundry, are equipped with a lower scalping deck and designed in accordance with heavy duty usage philosophy.
Our Wire Mesh Belt blast machines can blast work pieces that require a smooth or shockless pass through, such as flat, thin-walled, and fragile iron or aluminum alloy castings. Due to the position of blast wheels, bending of thin-walled work pieces and tilting of small light parts is avoided. Our machines are also designed to handle the high temperatures of work pieces that have been heat treated.
Pangborn Wire Mesh Belt blast machines provide high-volume, cost effective performance for deburring, cleaning, descaling, deflashing, and etching.

Wire Descaling Blast Machines
Pangborn Wire Descaling Blast Machines are designed for customers who want a versatile machine that can de-scale wire from 0.08 – 3.14 in (2 – 80 mm) in round, square, or hexagon shapes.
SandBlasting Systems & Spare Parts
Auxiliary Components

GenesisTM Blast Wheels
Pangborn GenesisTM Wheels Developed and supported by more than 100 years of blasting and cleaning experience, Pangborn’s Genesis family of blast wheels are revolutionary new wheels that offer significant savings and competitive advantages. The new Genesis technology takes ease of blast wheel maintenance to a whole new level—and drives savings straight to the bottom line. The blast wheel is an important variable that influences and determines the overall efficiency and operating cost of a blast cleaning system. Quality blast wheels must be durable, easy to maintain, and meet all performance standards. Pangborn offers the most versatile line of blast wheels in the industry including from 13″ (330.2 mm) to 26.5″ (673.1 mm) diameters, wheels with various speeds, vane, impeller, and impeller case designs that are used to handle the most challenging blast application. Regardless of the harsh conditions that exist within foundries, the high output requirements of automotive industries, or the exacting tolerances of peening specifications, Genesis Wheels are proving that they are not only one of the most technologically advanced wheels on the market, they are also the most versatile.

Abrasive Recovery & Seperator
In harsh blast conditions, a two percent (2%) volume of sands/fines in the abrasive can reduce the wear life of the internal wheel components by as much as 50%. Abrasive recovery and waste stream management are one of the most important aspects of your shot blasting system. Pangborn offers a complete line of abrasive recovery and waste stream solutions to meet any shot blast application. We work closely with our customers to understand their abrasive recovery expectations and how they intend to manage their end-of-life waste stream. A Pangborn solution can be incorporated into the design of new equipment, retrofitted on existing blast equipment (from Pangborn or a competitor), or delivered as a stand-alone system.

Dust Collectors
Pangborn has several dust collection systems that can be adapted to any manufacturer’s blast equipment and will effectively and efficiently evacuate dust and debris resulting from the blasting process. These all-inclusive systems require little maintenance and typically need only routine cartridge changes. We also offer dust cartridges to keep customers’ dust collection systems working at peak efficiency. The condition of the dust collector is critical to the proper performance of the separator. Blasting operations vary as do facility requirements. To find the proper dust collection system for your blasting operation, we encourage you to contact one of our specialists.

Loaders & Unloaders
Loading and unloading heavy parts can be both tedious and dangerous. It is often a time-consuming process and one that can be handled more efficiently using automation. Pangborn has several automation solutions for loading and unloading work pieces, including conveyor systems and hydraulic batch systems. These systems are easily fitted to existing blast equipment, regardless of the manufacturer. For safe and careful evacuation of blasted work pieces, Pangborn uses vibrating conveyers or rubber belt conveyers. In addition, all conveyors can be equipped with a weight capacity monitoring device. Pangborn has fitted hundreds of blast machines (Pangborn and non-Pangborn) globally with part loading and unloading systems. Whether you work in a rigid environment or are blasting fragile work pieces, we can help you determine the best loading and unloading system for your unique requirements.

Robot Handling Equipment
Pangborn uses state-of-the-art programmable robotic part manipulators to ensure every surface of the work piece is exposed to the blast stream for the correct amount of time. The customers who typically employ these types of systems are focused on making sure they have complete control over the part within the blast stream. Pieces handled in this manner are generally high-value items and/or are subject to precise tolerances. Pangborn builds high-performing systems that incorporate robot technology in order to guarantee sustained, consistent results, part after part. Pangborn is known globally for its commitment to technological advancements in wheel and air blasting. When coupled with an advanced work piece manipulation system, the result is a highly efficient operation that delivers accurate and repeatable results, part after part.

Shot Removal System
After blasting, some work pieces may retain difficult to evacuate residual abrasive. This typically occurs when blasting engine blocks or heads contained inside the water jackets and oil channels remain inside the castings after the blasting process is complete. This unexpected abrasive consumption is an economical loss for users of shot blasting equipment. Pangborn has developed shot removal systems that automatically evacuate all residual abrasive from the castings after blasting. Conveying systems for the total recovery of the abrasive are also available. Several options exist and vary based on customer requirements, including a fully automatic shot removal system with one rotational axis, a fully automatic shot removal system with two rotational axes for difficult parts as engine heads, and star type for high outputs up to 360 pcs/h. Pangborn helps customers identify multiple methods of lowering finished parts costs while ensuring each customer facility is as efficient as possible.
bottom of page